How To Make Chenille Patches: Step-By-Step Process, Equipments, And Tips
Chenille patches deliver a textured, vintage aesthetic that looks great on apparel, accessories, and even home decor. With their characteristic fluffy, raised surfaces, these patches are a staple on varsity jackets and tote bags.
In this guide, we walk you through how to make chenille patches with an embroidery machine. Whether you are a beginner or experienced with sewing, this post offers equipment recommendations and tips for making chenille patches that are durable and visually appealing.
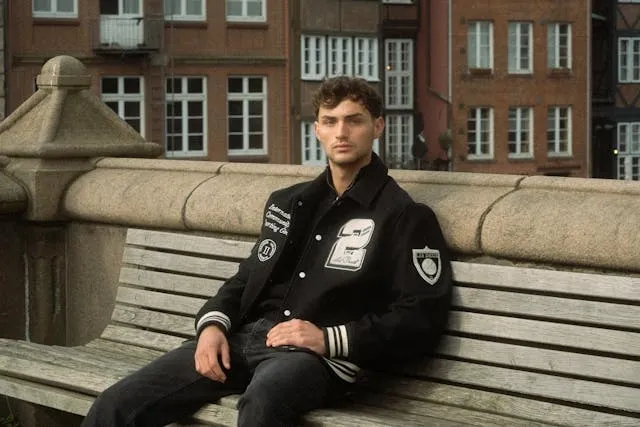
Key Takeaways
- How to make chenille patches involves using basic equipment, suitable stabilizers, and techniques tailored to chenille embroidery.
- The benefits of creating DIY chenille patches include creative freedom, personalization, and cost-effectiveness.
- You will need certain essential materials like chenille yarn, stabilizers, embroidery backing, and a reliable heat press.
- We supply high-quality custom chenille patches that offer flexible personalization options and a range of materials and attachment methods.
Table of contents
-
How To Make Chenille Patches
-
What Equipment And Materials Are Needed For Chenille Patches?
-
What Are Chenille Patches Made Of?
-
What Stabilizer Should You Use For Chenille Patches?
-
How To Apply And Maintain Chenille Patches
-
What Temperature Should You Use To Heat Press Chenille Patches?
-
How To Customize Letterman Jackets With Chenille Patches?
-
What Are The Steps For Making Chenille Patches DIY?
How To Make Chenille Patches
The first step in making chenille patches is to sketch your desired design, ensuring shapes and lettering are bold for optimal fluff and clarity. When ready, transfer this design to embroidery software or create it manually if you are crafting by hand. You will need chenille yarn to create the signature plush texture, combined with embroidery thread to detail the outlines.
Here’s the process for creation:
- Set up your embroidery machine.
- Insert the stabilizer and backing fabric into the hoop for a firm working base.
- Adjust machine settings to chenille stitching mode and ensure compatibility with your yarn thickness.
- Embroider your design, switching between yarn and thread as necessary for detailing.
It is also possible, but more complicated, to stitch yarn manually onto the backing material. Making chenille patches DIY is rewarding and allows complete creative freedom. You could also work with us to create custom chenille patches to your designs for accurate and cost-effective solutions.
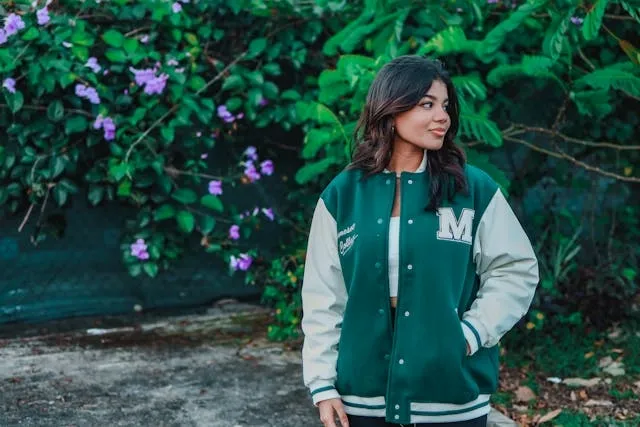
What Equipment And Materials Are Needed For Chenille Patches?
To craft chenille patches, you will need a combination of basic tools and specialized materials. From machinery to fabrics and additional resources, here are the things you will need:
- Embroidery machine: Yours will need to be capable of chenille stitching.
- Sewing machine: This can be necessary for the final assembly of your patch.
- Stabilizers: Whether tear-away or cut-away, these offer the necessary support during stitching.
- Backing fabrics: Felt, twill, or polyester make ideal bases for this.
- Chenille yarn: This is the primary material for adding texture.
- Embroidery thread: Use this for accent details like borders or logos.
- Adhesives: Options include fusible web or fabric glue to adhere your patch to a fabric.
- Additional tools: Make sure you have things like scissors, cuttings mats, and a heat press as needed.
For enhanced designs, software for creating patch templates is highly recommended. Having the right tools simplifies how to make chenille patches, as it does for how to make custom embroidered patches.
What Machine Do You Need To Make Chenille Patches?
As mentioned, an embroidery machine is a must-have for creating chenille patches efficiently. Researchers have collected datasets about defects in chenille yarn that may be helpful for detecting yarn that has problems before you use it. When choosing a machine, prioritize the following features:
- Compatibility with different hoop sizes.
- Chenille yarn functionality.
- Adjustable stitching speeds.
Entry-level models, like the Brother SE600, are beginner-friendly and budget-conscious, making it straightforward to learn how to make chenille patches with an embroidery machine.
For more advanced options, choose industrial-grade embroidery machines that offer higher stitching speeds, multi-thread compatibility, and digital pattern integration. And you can complement the work of an embroidery machine by using a sewing machine to finish edges or attach patches to garments.
With the right machines, you get accuracy and quality when making chenille patches.
Want to make a statement with your team's apparel?
Enhance your uniforms with our custom patches!
Order now and create unique uniforms with our high-quality, personalized patches.
What Are Chenille Patches Made Of?
Chenille patches are crafted using high-quality chenille yarn to achieve the signature textured, three-dimensional surface. Your backing material is a key choice, providing a study base to hold the intricate stitching.
There are two that stand out among DIY chenille patch makers:
- Felt: This is durable and easy to customize.
- Twill: Choose this for a sleek finish and high resistance to fraying.
Other essential components of chenille patches include embroidery thread for detailing and stabilizers to support the patch during and after embroidery. You will also need something like an adhesive backing or heat-activated glue for attaching your patch to garments, or you could just sew it on.
Combining chenille yarn, durable backing, and professional finishes makes chenille patches versatile and long-lasting. Our online store is an excellent source of custom chenille patches for sweatshirts. We offer flexible customization options, diverse materials, and competitive pricing to allow you to create your patches easily.
What Stabilizer Should You Use For Chenille Patches?
Using the right stabilizer is important to achieve a durable, professional finish when creating chenille patches. Two popular options are tear-away and cut-away ones:
- Tear-away stabilizers: These work well if yuo are working with fabrics that have minimal stretch, making it easy to remove when you have finished stitching.
- Cut-away stabilizers: These are great for stretchy or delicate fabrics, delivering long-term stability.
If you are creating intricate designs or working with lightweight materials, water-soluble stabilizers can deliver a clean, residue-free finish once they dissolve. Double-check stabilizer compatibility with your machine settings and patch materials.
When learning how to make chenille patches with an embroidery machine, always test your stabilizer on some scrap fabric. If you really don’t feel confident, consider options like our custom acrylic fiber beanies and other custom apparel to add personalized designs.
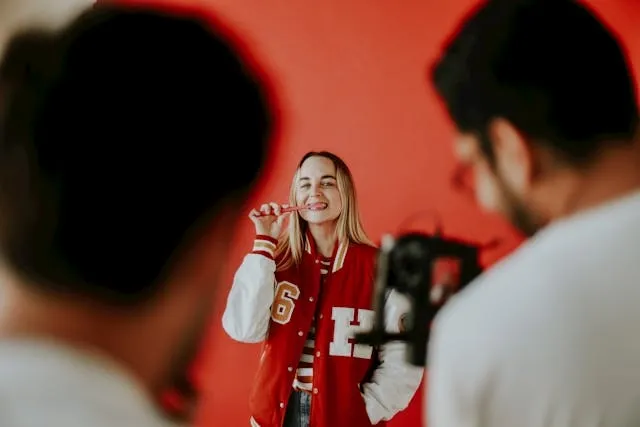
Stand out from the crowd with our unique designs
Customize your style with our patches!
Order now and make a statement
make your custom patchesHow To Apply And Maintain Chenille Patches
When you apply chenille patches correctly, you ensure they adhere securely to your garments or accessories for a long-term embellishment. The two most popular options are sewing patches on or attaching with iron-on backings.
- Sew-on applications: Use a zig-zag or straight stitch along the edges of the patch.
- Iron-on applications: Use a heat press or iron set to the proper temperature and apply pressure evenly for the recommended time.
Maintaining your patches is important and it doesn’t have to be complicated. We recommend that you hand wash or use a delicate machine cycle to avoid wear and tear. Avoid harsh detergents and high-temperature dryers as they may degrade the yarn or adhesives. With proper care, you can preserve the texture and longevity of your patches.
For an embellishment that is truly built to last, try designing a customized full-zip hoodie with our online service if you prefer to avoid patches.
How To Make Chenille Patches Stay On?
Effectively securing chenille patches takes proper adhesives or sewing techniques. Let’s look at what you can do to make different attachment methods as durable as possible:
- Iron-on: Heat-activated adhesives are quick and durable, and you can reinforce them with some sewing along the patch edges for enhanced longevity.
- Fabric glue: If you are using fabric glue to attach patches to fabrics like denim or leather, specialist fabric glues or industrial-strength adhesives deliver a strong attachment.
- Sewing: Choose heavy-duty thread and a zig-zag stitch to cover the edges and prevent unravelling.
Avoid overhandling freshly-adhered patches. For instance, how long iron-on patches stay on depends largely on the application method and what you do immediately after the application. Regular care and good application techniques will keep your chenille patches securely affixed.
What Temperature Should You Use To Heat Press Chenille Patches?
If you are using a heat press to apply your chenille patches, we recommend that you set the temperature within the following range:
- 320–340°F
- 160–170°C
Adjust the pressure and time based on the materials involved. If you have a thicker backing, you may need a longer press time. Make sure you implement a protective sheet, like thin cloth or parchment paper, to prevent direct contact between the patch and the heat press.
For delicate materials, an iron may be a gentler alternative. It is straightforward to iron on patches, but the results may lack the uniform adhesion you achieve with a heat press. Always test on scrap fabric to determine the optimal settings in either case. Proper temperature ensures secure bonding without harming the chenille texture.
Add a personal touch with our custom patches
Express yourself with our wide range of designs
Order now and make it yours.
How To Customize Letterman Jackets With Chenille Patches?
Adding chenille patches to a letterman jacket is a classic, personalized look that we often see on school and college varsity jackets. Placement is important for this, and your choice should depend on the type and size of the patch. Popular placement locations include:
- Chest
- Back
- Sleeves
Your patch designs could incorporate initials, logos, or symbols that stand out. Choose bold colors or opt for more subtle designs to give it a modern twist.
It is quite straightforward to put patches on a letterman jacket, and you can incorporate layered patches with different textures to create depth. Alternatively, you could embellish with embroidery or additional trims to add character. A sewing machine makes it simpler to add patches seamlessly to jackets, but you determine the correct method based on the backing of your custom chenille patches.
What Are The Steps For Making Chenille Patches DIY?
Creating chenille patches at home is an engaging and rewarding project. It involves drawing the patch pattern, stabilizing the patch, then setting up the fabric in the machine hoop before using the embroidery machine.
Whether you’re crafting for fun or seeking to enhance your garments, this DIY method allows for creative freedom. Follow the clear step-by-step guide in the subsequent section to design, stabilize, and embroidery patches with professional results.
Making chenille patches DIY is a cost-effective and accessible approach, particularly if you are passionate about crafting. If you are not bothered about the DIY touch, you could work with us to create custom large chenille patches with your bespoke designs for a high-quality finish.
Step 1: Drawing The Patch’s Pattern
Start by sketching the design on paper or use graphic design software. Simple bold shapes are best to take maximum advantage of the chenille texture, so avoid overly intricate details. Create clean outlines with tools like:
- Rulers
- Compasses
- Stencils
If you are a beginner, trace a template or download a ready-made pattern for accuracy. Transfer your finalized design onto stabilizer paper or directly onto fabric using water-soluble pens. The aim is to create a clear, well-defined pattern optimized for chenille embroidery.
Step 2: Stabilize The Patch
Stabilizing your fabric is a crucial step to ensure durability and maintain the shape of your patch. Choose a stabilizer based on your fabric for best results. On sturdy materials, tear-away stabilizers are a good choice, while cut-away options are best for stretchier fabrics.
You can attach the stabilizer with an iron or adhesive spray, depending on the stabilizer type. Make sure you secure the fabric-stabilizer layer tightly before you move forward. Proper stabilization prevents puckering and ensures your design stitches cleanly during the embroidery process.
Step 3: Attach Fabric To The Machine Hoop
Properly setting up the fabric in your embroidery hoop is key if you want a smooth stitching process. In industrial settings, research has shown that optimizing special parts and loom processes are key to ensuring successful production, and the same goes for home creation.
Here are some tips:
- Place the stabilized fabric over the inner ring of the hoop and secure it with the outer ring.
- Adjust the tension screws to keep the fabric taut but don’t over-tighten as this can distort the material.
To ensure even stitching, we recommend that you test your setup by running a quickl outline stitch. The design should remain centered within the hoop area to avoid alignment issues. With a properly hooped fabric, you simplify making chenille patches and ensure the end results has clean, professional-quality edges.
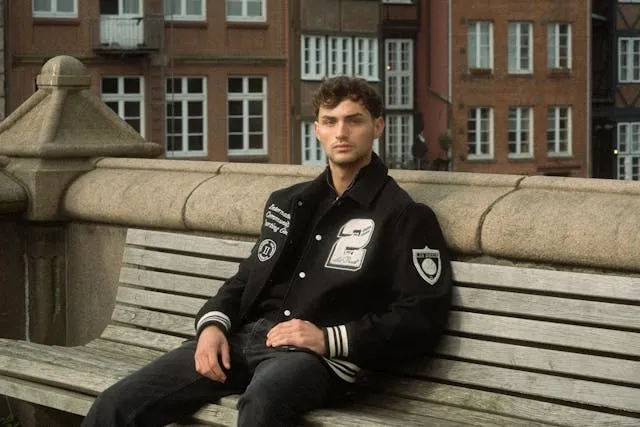
Make a statement with our unique designs
Stand out with our custom patches!
Order now and show off your style
make your custom patchesFrequently Asked Questions About How To Make Chenille Patches
How To Make Chenille Patches With Embroidery Machines?
To make chenille patches with an embroidery machine, you need to digitize your design and load it into the machine. You must then prepare the fabric and stabilizer before embroidering the chenille yarn using chenille stitching settings, alternating with thread for detailing.
Can You Use A Heat Press For Chenille Patches?
Yes, a heat press is ideal for adhering chenille patches with a heat-activated backing. In most cases, the ideal temperature is between 320–340°F and you should use even pressure to bond the patches securely.